After looking for "uppers" for one of my TC contenders for my Daughter and not liking the prices I decided to build them.
Started with the .22 blank and turned it down and threaded it for a suppressor.
While I was at it, I went ahead and machined a thread protector if it ever didn't have one on or a QD adapter on the threads.
After a little searching, I couldn't find any weld on lugs (one source for threaded) and machined my own just averaging the measurements from the TC barrels I do have.
Welded the first one together yesterday, chamber reamer is on the way now and after that will have to machine the slot for the extractor, finish and test. If it is a "winner", will do the next one the same way.
Started with the .22 blank and turned it down and threaded it for a suppressor.
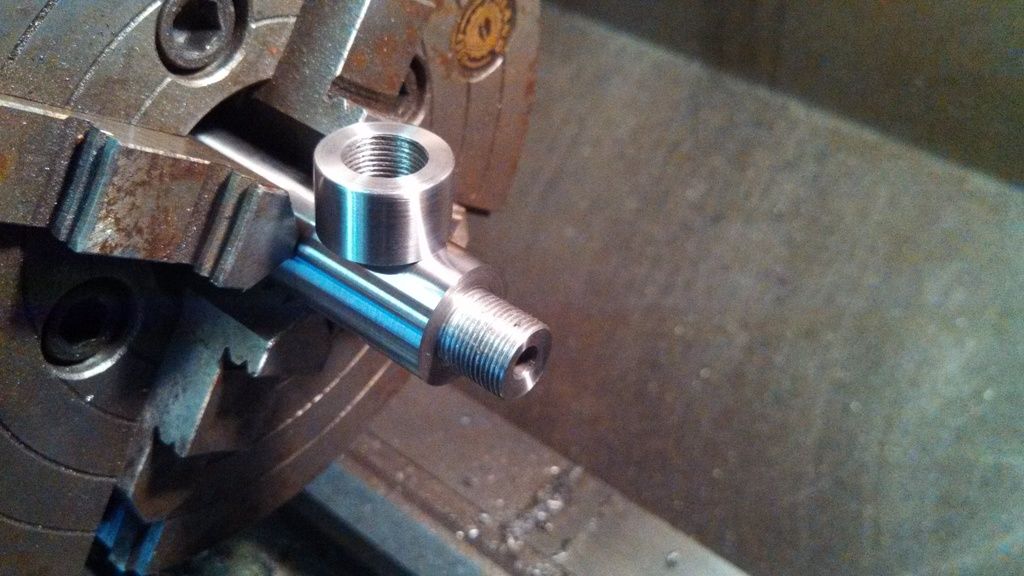
While I was at it, I went ahead and machined a thread protector if it ever didn't have one on or a QD adapter on the threads.
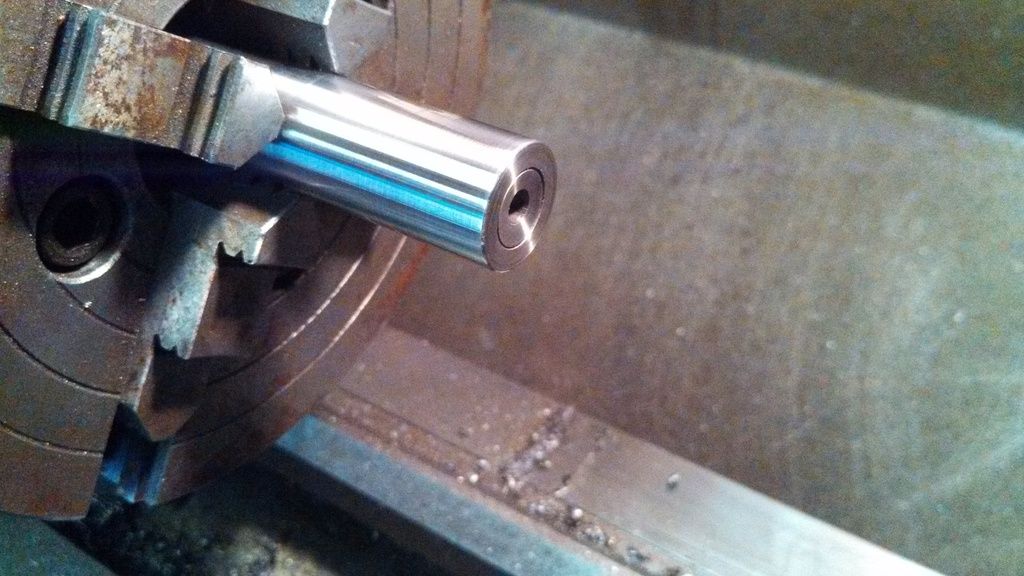
After a little searching, I couldn't find any weld on lugs (one source for threaded) and machined my own just averaging the measurements from the TC barrels I do have.
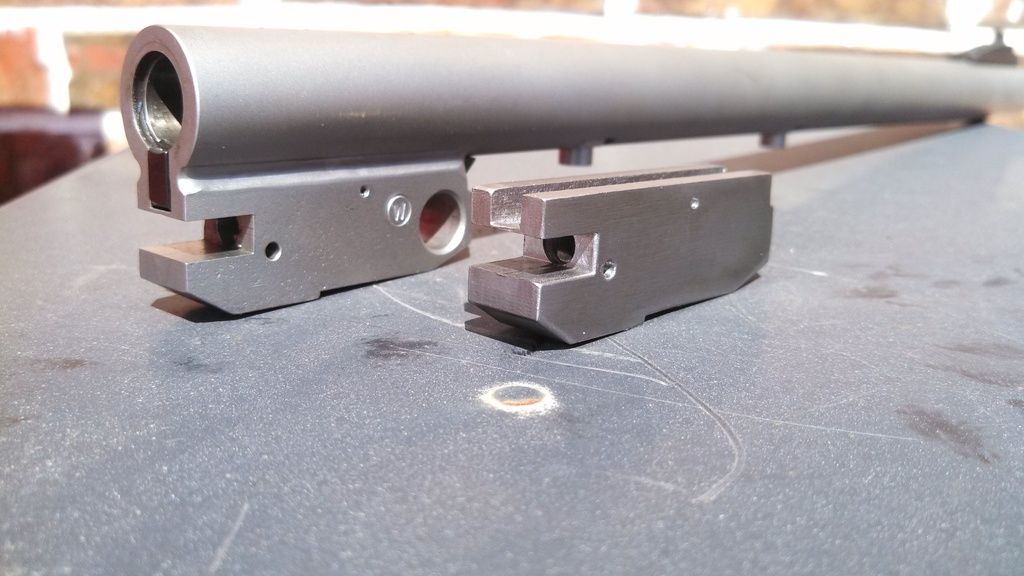
Welded the first one together yesterday, chamber reamer is on the way now and after that will have to machine the slot for the extractor, finish and test. If it is a "winner", will do the next one the same way.
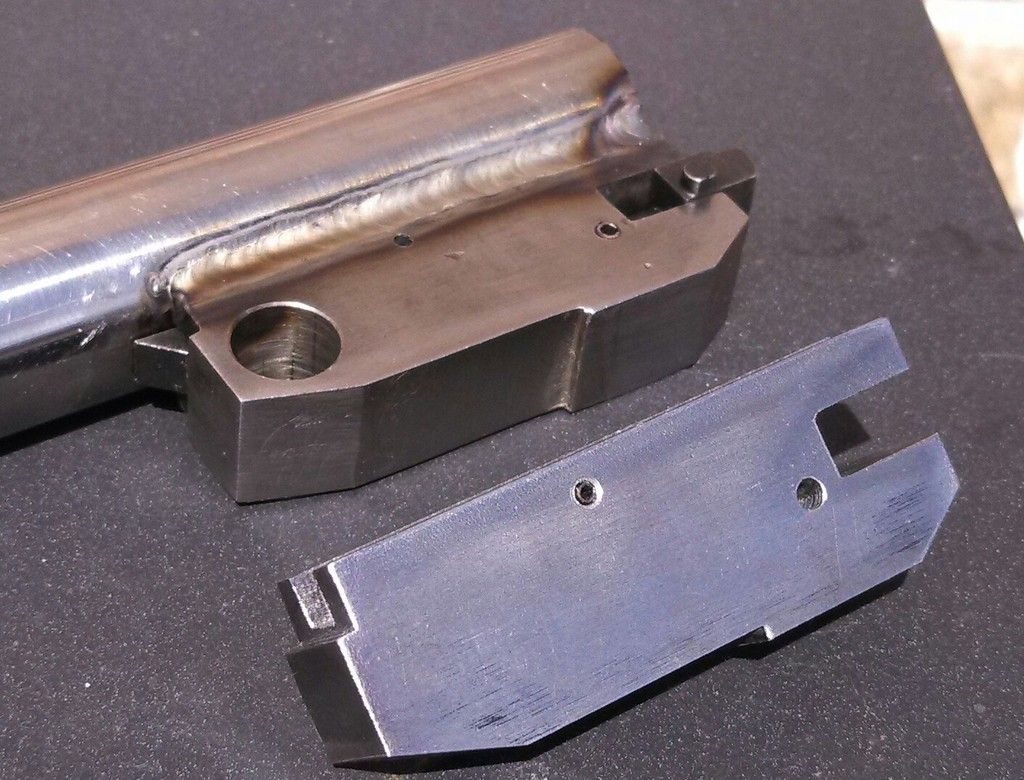